Metal Spinning is a process by which a disc or tube of ductile metal is rotated on a spindle and formed into an axially symmetric part. Through the use of heavy forces and high speeds, the metal will deform and “flow” to form the desired shape around a mandrel, a kind of mold that is shaped to the interior geometry of the planned part. This process allows metal to deform evenly, without any wrinkling or warping, to create a smooth, even, and seamless surface. The processes’ heavy forces also realign and strengthen the grain structure, significantly increasing the tensile properties and fatigue resistance of the base material.
Metal Spinning offers a series of compelling benefits for prototype and specialty work. High precision tolerances are easily attained on a wide variety of metal materials and designs. Mandrels are easily manufactured using traditional lathe and mill work, and considering that they are not subjected to excessive force in normal use, may be made of nonmetal materials. CNC control, hydraulic assistance, heat for hot working, and toolholders can all be incorporated into the metal spinning process. Overall, Metal Spinning permits an unparalleled level of flexibility, speed, and efficiency without sacrificing the precision and accuracy delivered by traditional processes.
For designs that are not conducive to spinning operations, Metal Hydroforming provides similar benefits and efficiency gains, effectively replacing work performed by machining or dies. The sheet hydroforming technique replaces one of the rigid dies used in conventional stamping with highly pressurized hydraulic fluid, contained by a urethane diaphragm, to force the sheet metal into a one-sided die cavity. Since the diaphragm, which is essentially acting as the female die, has no distinct shape, its dynamics allow it to take on the shape of any conceivable geometry. Complicated shapes with concavities are now possible in a single press cycle, reducing the amount of follow-up work and required forming operations. Produced to net shape, a single hydroformed component can often replace multiple parts, resulting in assemblies with fewer parts, higher strength, and less cost.
Metal Hydroforming brings many advantages over the typical die press processes that it replaces, especially in the context of prototype and specialty work. New part designs only require replacement of the lower die, which is usually made of cheaper cast iron and not expensive tool steel. During pressure application, friction and stress on the sheetmetal is significantly diminished, resulting in more consistent stressing and increased material drawability. Supplemental finishing operations are not necessary as the material is not marred as it is in standard die operations. Simplicity, efficiency, and service life are all upgraded significantly with Metal Hydroforming.
With the combination of these two processes, a new, and far better, system for prototype and specialty work is realized. Metal Spinning and Metal Hydroforming provide a definite pathway for one-off productions, design formulation, scratchwork, and design qualification, and simultaneously provide a full replacement for expensive, time-consuming traditional methods. Furthermore, both processes may work with just about any cold formed metal, and are easily reconfigured for high production work without any sacrifice in quality. Once the prototype becomes the new product, Metal Spinning and Metal Hydroforming are flexible enough to become the manufacturing system for it.
Helander is an experienced provider of those two services, able to add Metal Spinning and Metal Hydroforming capability to your production paradigm. Helander’s engineers, manufacturing technologists, and material specialists can provide in-depth analysis of component design, advise you on the feasibility and practicality of using metal spinning or hydroforming to form your component part, and can completely manage the production thereof within their state-of-the-art manufacturing facility. Contact us today to let us help you decide what’s best for your bottom line.
Want to know more?
Download our latest eBook Metal Spinning and Hydroforming - The Stamping Alternative.
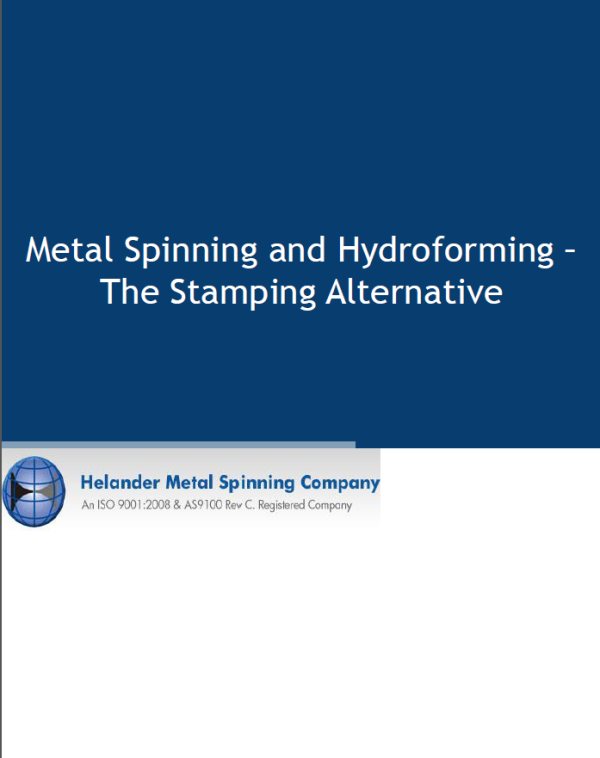