The metal spinning process consists of a tube or a disc of metal that is rotated at high-speed and machined into an axially symmetrical product using either a vertical or horizontal lathe. The advantage of spinning over other forming processes is its capacity to create seamless products from a single piece of material, with relatively low-cost tooling. Without seams, parts can withstand much higher internal and external pressures.
You will typically find spun metal components in decorative and architectural parts. Spun metal parts are also featured in variety of machines, cookware, gas cylinders, and brass instruments, and can be made from a variety of materials. Let's discuss the three most common materials for spinning.
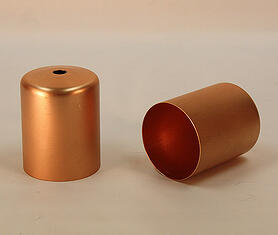
When considering material choices for spun parts, the most important factors are cost, the finished part's desired shape, and the application. It is well known that commodity prices fluctuate based on global supply and demand forces, fuel prices, and input material costs, but steel is generally a cheaper option than most other metals.
Steel is an extremely durable material, and much harder than aluminum. Its strength makes it less prone to warping, deformation, and bending under high forces or heat stress. Moreover, steel is a very dense material. In fact, it is 2.5-times denser than aluminum. This ensures that steel spun parts will not dent or scratch easily.
Aluminum
While aluminum is generally a more expensive option, it is more malleable and elastic than steel. It can therefore be used to create shapes with deeper and more intricate features – shapes that would end up cracking or ripping if spun with steel.
In addition to its malleability, aluminum is naturally resistant to corrosion and does not rust, and therefore it does not require any surface treatment after spinning. Since coating/painting is not required, you do not have to worry about scratching and surface wear, exposing the part to corrosion. This makes aluminum the natural choice for wet or abrasive environments.
Copper
Copper, along with steel and aluminum, is one of the most commonly used materials in metal spinning. It is non-magnetic, versatile, and aesthetically appealing. Typically, copper is a more expensive option than aluminum or steel.
It is particularly known for its exceptional thermal and electrical conductivity, corrosion resistance, high ductility/workability, recyclability, and antimicrobial natural. Interestingly, its tensile strength actually doubles when work-hardened. Moreover, copper is a soft metal that is easy to work with.
Copper spun parts are often used for lighting, medical equipment, pipes and sinks, roofing, and decorative applications such as jewelry.
Other Metals
In addition to steel, aluminum, and copper, Helander also manufactures spun parts using a variety of other metals such as Inconel, Hastelloy, titanium, bronze, and brass, each with their associated pros and cons.
Metal spinning is often the best choice for symmetrical parts because of the seamless construction, low-cost tooling, and low levels of wasted material. A variety of metals can be formed into spun parts: the right choice depends on the cost requirements, the shape of the part, and the working conditions.
Steel is a low-cost material offering high strength and durability, while aluminum permits more complex part shapes and a greater resistance to corrosion. Copper is like aluminum in many ways, but is typically more expensive. For this reason, copper is often appropriate for applications where its aesthetic properties outweigh its high cost.
Want to learn more?
Contact us to learn more about our metal spinning capabilities and the various material options for your application, or check out our newest eBook, 5 Metal Spun and Hydroformed Items that Required Surface Finishing, to learn more about how we can assist in your project from start to finish.